Local Exhaust Ventilation
Introduction
Local Exhaust Ventilation controls air contaminants by inhaling them from workplace and also to maintain control of hazardous substances (physical hazards i.e., fumes, dusts, smoke, heat, etc.) at a levelled exposure levels within the workplace exposure limits (WELs) to protect the workers. LEV controls highly toxic contaminants before they reach at workplace or workers. LEV is also known as Local Exhaust System.
LEV can control:
- air contaminants,
- large amounts of fumes / dusts,
- and provide breathing zones at workplace.
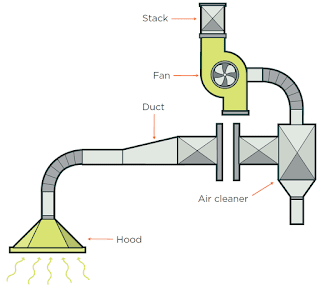
LEV has five elements:
- The hood that captures the contaminants at the workplace.
- Ducts that bring the airborne chemicals through the system and air that circulates again.
- An air cleaning device that takes away the contaminants from the moving air in the system.
- Fans that blow away the air through the system and discharge the exhaust air.
- An exhaust slack that discharges contaminated air.
Advantages of LEV
- Captures contaminants at workplace and remove it from the workplace.
- Require measurable maintenance.
- Energy costs is less and output is optimum.
Disadvantages of LEV
- Higher cost for installation, design and equipment.
- Require regular inspection, cleaning and maintenance.
COSHH Risk Assessments
Post implementation of Control of Substances Hazardous to Health Regulations 2002 (COSHH), Employers and Management must performs the COSHH Risk Assessments to reduce the exposure at a required level.
- Visual observations (i.e. safety rounds, tours, etc.) and checks (i.e. inspection, audits, etc.) to be carry out at appropriate intervals (once every 14 months).
- Schedule routine checks (daily/ weekly/ monthly) by competent personal (i.e., Safety Officer, Safety Manager, etc.).
- Monitoring system for the efficacy of controls and immediate remedial action where necessary.
Hierarchy of Controls
Many companies still believe that any potential circumstance where the generation of an airborne contaminant may happen requires the automatic application of LEV. This shows a lack of understanding of the importance of the hierarchy of control and misses out on vital considerations, such as limiting the rate and process change.
- Elimination of dangerous substances.
- Substitution by a material less hazardous.
- Use of engineering controls at source, including LEV.
- Administrative controls such as work procedures and organizational measures.
- Individual protection measures including personal protective equipment (PPE).
Based on the controls as mentioned above, LEV should only be considered at step three, after the likelihood of substitution and elimination have been addressed.
There are following things to consider when developing an efficient process to aid control of contaminants:
Access to the work area
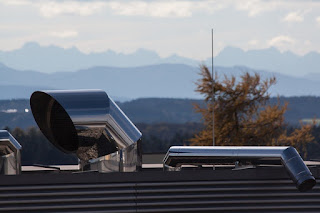
- Only authorized, competent and properly trained worker should have access to the work area.
Equipment & Procedures
- Apply LEV enclosed to workplace that inhales airborne contaminants.
- Airflow must be adequate to control airborne contaminants depending size of opening, design and types of substances.
- Have clean air supply coming into the work environment to restore extracted air.
- Do not allow the worker to come in between the LEV and source of exposure. This will makes them directly in the path of the contaminated airflow.
- Offer an easy way to check if the LEV works.
- Discharge extracted air to a secure place away from windows, doors and air inlets.
- Recirculate clear, clean, filtered air in to the room.
- Recirculation is not recommended with vapours.
- Make sure that all elements are appropriate for the captured substances.
- Human body which may effect due to exposure (i.e. skin, eyes, etc.) to be covered by suitable PPEs as instructed or advised.
- Talk with your supplier about the proper protective equipment.
- Make suitable arrangements for storage, maintenance and replacement of PPE.
Personal Decontamination
- Provide creams that make it easier to wash the dirt off the skin.
- To provide warm water, soft fabric towels and mild skin cleaners. Avoid abrasive cleaners.
Maintenance, Examination and Testing
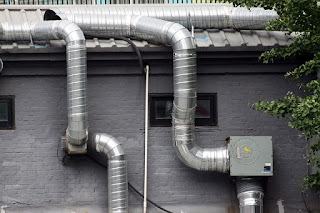
- Maintain and keep all your equipment in good working condition.
- Check for damages to control equipment prior starting work.
- Follow special procedures (i.e. operating instructions, SOP, reference manual, etc.) prior opening exhaust system.
- Allow a competent person to check the thorough examination and test at least every 14 months.
Cleaning and Housekeeping
- Clean work equipment and area daily at least once a week.
- Use wet cleaning methods or vacuum dry dust.
- Use suitable protective gloves to clean up spills. You may also use a piece of respiratory protective equipment (RPE).
- Safely dispose of empty containers and store containers in a safe place.
Training & Supervision
- Make sure that employees follow work procedures.
- Share potential hazards and risks with workers at workplace.
- Consider keeping training records.
- Changes to the LEV (i.e. updated installations, etc.) might mean re-training.
- Involve supervisors and managers in Health & Safety training.
Essential points to be considered during Installation
- The LEV system should be leak-proof. Leakage on the side of the suction leads to inefficient extraction and may reintroduce contaminants to the workplace.
- The flow rate of air through the system must be adequate to achieve the initial inhaling, so that system can carry contaminants to the filtering system (to avoid combustible clouds of dust may get deposited in the duct results explosion or fire risk).
- The structure of ducting to be ensured during installation (i.e. it should not have right angled turns as this leads to dead ends with no flow).
- The materials and construction should be compatible with the contaminants (i.e. the LEV system should not generate a source of ignition). Corrosion by contaminants is another issue to contend.
- Make sure that the hood is as near to the workplace and process.
- Put the hood to benefit form the direction and speed of the airflow from the workplace.
- Separate the breathing zone of the worker form the contaminant cloud.
- Limit eddies within the hood.
- Use ergonomic principles and ensure consistency during designing the application of an LEV hood.
- Match the LEV control effectiveness to the degree of over-exposure based on the capabilities of various types of designs and hoods and how exposure occurs.
- Specify the volume of flow from each hood in a custom design.
- Establish the total pressure at each junction and the flow rate.
- Plot the design in standard-size ductwork.
- Some calculations to be considered:
- Air density.
- Air velocity from the pressure difference.
- Circular duct cross-sectional area.
- Maximum vapour concentration for a liquid.
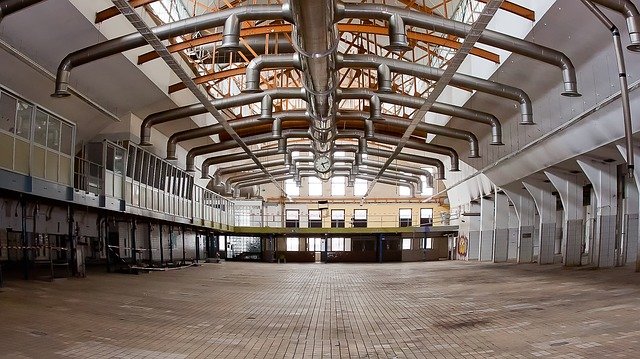