Helmet
Helmet is one of the most vital PPEs used by workers to prevent head injuries which may be caused by falling objects in most of the industries (i.e., mining, ship building, construction projects, tunnelling, etc.). Accidents such as head injuries caused by falling objects are usually serious and sometimes fatal.
Safety Helmets or Hard Hats are designed to provide protection against strong head impact, electrical injuries and penetration injuries which may cause near miss or accident by falling or flying of heavy objects.
Initially leather helmets were used before World War I and during such Edward W. Bullard invented metal hats (i.e., hard-boiled hat, black painted with canvas & leather headgear) came in force in 1919. In 1938, metal hard hats were introduced which was not for electrical applications. Fiberglass came into use in 1940s.
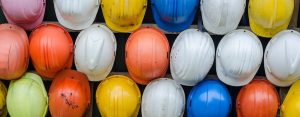
Definitions
- Shell: Shell is the hard smoothly finished material that provides the general outer form of the helmet.
- Peak: Peak is the extension of the shell above the eyes.
- Brim: Brim is the rim surrounding the shell.
- Harness: Harness is the complete assembly from which the helmet is maintained in position on the head, which includes headband, cradle, etc.
- Headband: Headband is the part of harness which is surrounded by the head. The plane of lower margin of headband shall come in the line of the head from and the headband may or may not be continuous when Naper strap is provided. Sweatband is attached with headband in the front side where forehead comes.
- Anti-concussion Tapes: Anti-concussion tapes supports straps which forms cradle. It also acts as shock absorber when any object falls from height.
- Cradle: Cradle is the fixed or adjustable assembly comprising of anti-concussion tapes and nape strap.
- Chinstrap: Chinstrap is an adjustable strap that fits under the chin to secure the helmet on the head.
- Nape Strap: Nape Strap is an adjustable strap that fits behind the head to secure the helmet which is considered as an integral part of headband.
- Ventilation Holes: Ventilation holes provided in the shell to permit circulation of air inside the helmet.
Briefs
The surface of the helmet shall be finished smooth, free from burrs or sharp edges which should be removed to ensure proper surface contact of the fittings. The shell of the helmet should made up of non-metallic materials (i.e., conforming after trail tests).
The criteria for the selection of material for the headband, anti-concussion tape, etc., should be sweat-resistant and non-irritant which should not result to skin disease. The metal parts used (if any) in helmets shall be corrosion resistant.
Helmets are manufactured in sizes i.e., 520 mm, 530 mm, 540 mm, 550 mm, 560 mm, 570 mm, 580 mm, 590 mm and 600 mm. The size adjustment range is clearly marked on the helmets. A tolerance of +10 mm on the size of the headband shall be permitted.
The size of headband should be measured with either a fixed ring gauge or an expanding gauge which shall be made of metal. The weight of a helmet without attachments (i.e., with or without peak) may not exceed 400 grams.
The life of helmet, manufacturer’s name or trademark and range/size are provided in inner side of helmet. The helmet should also be marked with the ISI certification mark.
Construction
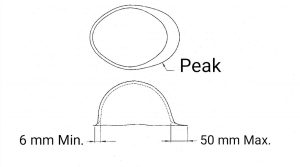
Shell
The shell is a dome-shaped, protection equipment without any sharp edges. There should not be any metallic component passing through the shell. Shell should be provided with a brim, with or without peak. The brim and peak are integral part of the shell. The position of ventilation holes should be almost horizontal when the helmet is in wearing position. The diameter of any hole shall not exceed 6 mm. The distance should be not less than 3 mm between two holes.
Harness
Headband should be not less than 30 mm in width and should be adjustable. Headband should be attached properly with the shell and straps. The minimum distance of headband from shell should be 5 mm to provide ventilation.
Cradle
The headband should be fitted with anti-concussion tapes at 4 anchoring points at least. The width of strap shall not be less than 19 mm. The strap should have a clearance of at least 30 mm from the top of wearer’s head and inside of the top of the helmet crown.
Chin Strap
Chin strap should be attached to the shell and should be at least 19 mm wide. It should be permanently fitted with a fastening source to adjust and maintain tension and fulfill the requirements.
Nape Strap
Nape strap is attached to headband from behind and have a minimum depth of 115 mm.
Performance Tests
Prior distribution of manufactured safety helmets has to undergo performance tests as per policy laid by Govt authorities. Performance tests for safety helmets are as follows:
- Shock-Absorption resistance: Helmets are tested for shock absorption for not higher that 5kN (510 Kgf).
- Penetration resistance
- Flammability resistance: The material of the shell shall not burn with emission of flame after a period of 5 seconds following removal of flame.
- Electrical resistance: Helmets are tested to absorb a leakage of current in excess of 3 mA.
- Water absorption: Helmets cannot absorb water more than 5 percent of its mass.
- Heat resistance
Color & Identification
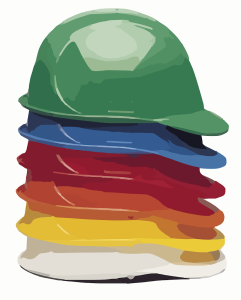
- Green helmets: Normally worn by safety professionals (i.e., Safety Officer, etc.).
- Blue helmets: Worn by carpenters and technical operators.
- Red helmets: Worn by firefighters and electrical staff / operators.
- Orange helmets: Worn by road crews, signalers, operators in lifting operations and new employees.
- Yellow helmets: Worn by foreman, labors / workers and earth-moving operators.
- White helmets: White helmets are worn by superior authorities, managers, engineers, supervisor, etc.
- Brown helmets: Who are engaged in welding and high temperature workplaces wear fiberglass helmets.
- Grey helmets: Worn by site visitors.
Types
Class A helmets
Class A helmets offer users with impact and penetration resistance apart from limited voltage protection (up to 2200 volts).
Class B helmets
Class B helmets offers the best quality of protection against electrical hazards (i.e., electrical safety) with high-voltage shock and burn protection. They also protect users from impact and penetration hazards caused by flying / falling objects.
Class C helmets
Class C helmets on the other hand offer lightweight comfort and impact protection. However, they cannot check electrical hazards.
Given below are some the different types of helmets that have gained popularity in recent times:
- Nape helmets: The inner shell of this type of helmets is normally made from plastic. These helmets are often used in mines and are equipped with a comfortable strap. They have a bright, shinning surface.
- Rachet helmets: The headband of these helmets is created soft on irritant fabric to offer a high level of comfort to the worker. Universal adjustment is ensured by the adjustable chin strap. The shell’s triple corrugation guarantees a high level of impact resistance.
- Without Rachet helmets: These helmets are electrically insulated for working in low voltage environments. They are ideal for use in temperatures.
- Safety Helmet, Explorer I: Created from UV-resistance ABS material, this helmet has good absorption and can resist high impact. This safety helmet is mainly available in ratchet adjustment, tape and plastic suspension lining harness. The helmet fits users with the head size between 53 cm and 66 cm.
- Industrial helmet: These helmets come with a slide lick system which makes them easy to use.
- Safety helmet, HM2: These types of safety helmets are light, comfortable and offer workers with a satisfactory quality of ventilation. Their hard shell has been created UV-resistant ABS or HDPE materials which are good absorbers and resists high impact effectively.
- Fiber Glass Safety helmets: The safety helmets of this types offer wearer with a high level of comfort and functionality. They keep the wearer’s head safe from direct impact and penetration caused by falling or flying object while using grinding machine or any hot work.
DO’s
- Do follow the guidance and regulation of helmet as briefed by Safety Officer during toolbox talk.
- Start your work only after wearing your helmet to prevent yourself
- Check your helmet for any signs of any damage. If any damage found, then replace it.
- Wear helmet right way around.
- Secure your headband and chin strap under the chin and fastening it adequately as required to ensure safe working practices.
DON’Ts
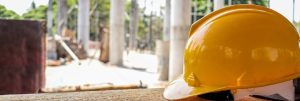